Envision
How can businesses be better prepared for periods of supply chain disruption
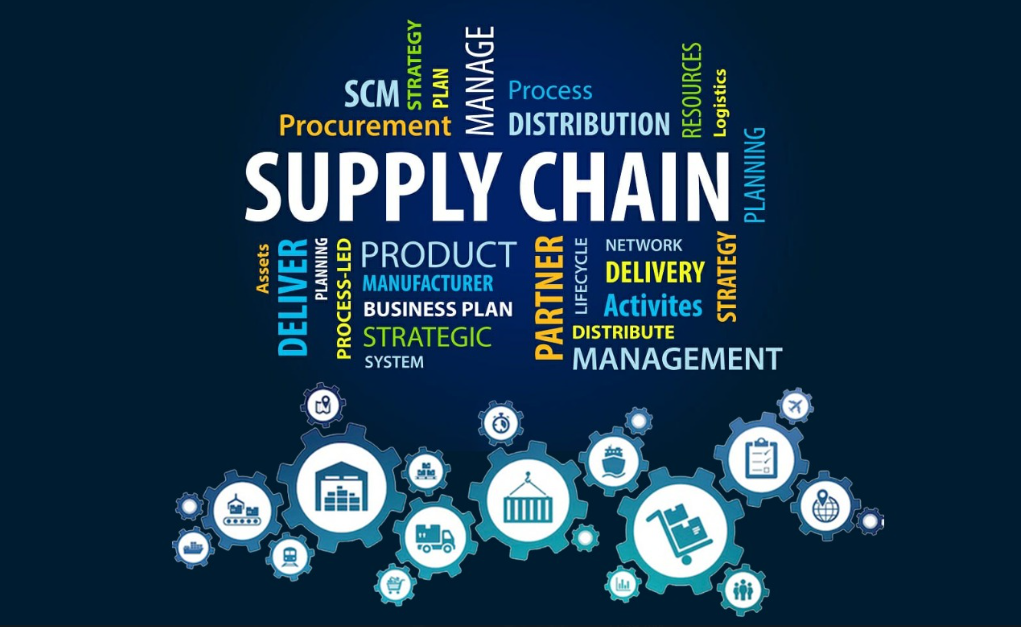
Capitalism has accelerated the transmission of diseases. Historically, most epidemics have spread geographically through two common forms of human long-distance movement : trade and war. The timing, however, changed dramatically with the rise of capitalism.
In the Middle Ages, it took a decade or so for the Black Death (bubonic plague) to spread from China via the Silk Roads and Mongol conquests to Europe. Then, years to move from Sicily to Britain and beyond, via established trade routes and the movement of armies during the Hundred Years War. With capitalism well established, the “Spanish Flu” of 1918 spread in months from Spain, through France to Britain by Mid-June, and then to the US and Canada in September. To a large extent, it followed the course of battle lines, troop movements, and military logistics during WWI.
In the era of just-in-time logistics, it took the corona virus mere days to spread from Wuhan to other Chinese cities hundreds of miles away. It took only two weeks to move beyond China, simultaneously along major supply chains, trade, and air travel routes to the industrial and entrepôt enclaves of East Asia, the war-torn,oil-producing Middle East, and industrial Europe, North America, and Brazil.
As MIT logistics guru,Yossi Sheffi, pointed out in The Power of Resilience, “The growing interconnectedness of the global economy makes it increasingly prone to contagion. Contagious events, including medical and financial problems, can spread via human networks that often strongly correlate with supply chain networks.
It is estimated that 51,000 companies around the world have one or more direct suppliers in Wuhan,while 938 of the Fortune 1000 companies have tier one or two suppliers in the Wuhan region. The emphasis for the last two or three decades on lean production, just-in-time delivery, and, more recently, “time-based competition,” along with updated transportation and distribution infrastructure, has accelerated the speed of transmission.
The COVID-19 pandemic has disrupted nearly every part of supply chain, from supply upstream to inbound and outbound logistics to demand planning and forecasting.
The outbreak is arguably more impactful than all these events combined because it hasn’t just created hurdles, it has completely stopped production, something many supply chains can’t absorb.
But the reasons businesses are struggling to deal with the fall out are the same: supply chains are fragile.
The main reasons are :
Reduced inventory levels :
Just-in-time manufacturing allows companies to increase efficiency and lower the cost of their supply chain, but it also leaves supply chains less resilient to sudden shocks and supply shortages.
Rigid supplychains :
This wouldn't be a problem if businesses operated flexible supply chains. That way they could switch order volumes to alternative suppliers in times of stress. However, very few companies don’t do this, leaving them unable to identify and connect with alternative suppliers when there are sudden shocks to their supply chain resulting in a tangible impact on production.
Manual supply chain management :
A key reason that supply chains are rigid is because they’re managed manually. Making changes to orders or shifting suppliers is a lengthy and complex process and in times of stress is a luxury few companies have.
Lack of supply chain transparency :
Businesses are often unaware of what’s happening across their supply chain beyond the first tier, so they’re unable to know where threats to production capacity exist. And this makes it near-impossible to proactively manage a situation like the COVID-19 outbreak.
Consolidated centers of production :
The globalization of supply chains has led to the development of specialist production zones—cities or countries specialize in the production of a few key products. These have helped ensure there is a plentiful supply of key supplychain components and lowered the overall cost of supply. Yet while this is beneficial when times are good, it can cause issues when there is disruption. That’s because there isn’t the capacity in other parts of the world to plug the gap in supply.
So how can businesses be better prepared for periods of supply chain disruption ?
Immediate needs are the most urgent:
Keep employees safe while maintaining essential operations. Implement operational safety measures, such as alternating crewing patterns, remote work readiness and Q&A hotlines.
Now businesses are beginning to also think about strategies to build resilience in the medium termand adjust to a "new normal" beyond the pandemic.
Create transparency on multi tier supply chains, establishing a list of critical components, determining the origin of supply, and identifying alternative sources.
Estimate available inventory along the value chain—including spare parts and after-sales stock—for use as a bridge to keep production running and enable delivery to customers.
Assess realistic final-customer demand and respond to (or, where possible, contain) the shortage-buying behavior of customers.
Optimize production and distribution capacity to ensure employee safety, such as by supplying personal protective equipment (PPE) and engaging with communication teams to share infection-risk levels and work-from-home options. These steps will enable leaders to understand current and projected capacity levels in both workforce and materials.
Identify and secure logistics capacity, estimate capacity and accelerate, where possible, and be flexible on transportation mode, when required.
Manage Cash and net working capital Preserve cash. Manage the inflow of the material, right-size inventory, bolster creditand collection, control the payments outflow.
Once the immediate risks to a supply chain have been identified, leaders must then design a resilient supply chain for the future.
Build ingresilience for the future
The question of supply chain resilience can be addressed in different ways. One way to ensure greater supplychain resilience is to move more manufacturing and assembly close to the headquarters. This, of course, is reversing the nature of the globalization that we have seen in the past decades, but for some companies, this is worth serious consideration.
There is a lot of talkabout robust supply chains. Anti-fragility takes this a step further.Anti-fragile supply chains aren’t just strong, they’re malleable to ensure they continue working no matter the disruption. But, most crucially, they don’t just survive the disruption—they improve because of it.
To get there, businesses need to go digital. It sounds elementary to say this in 2020. But the fact is paper and manual process power most supply chains. And there is zero chance of building a robust supply chain, let alone one that’s anti-fragile when buyer sand sellers aren’t digitally connected.
Making this digital connection is the foundational element for building an anti-fragile supply chain. Once this happens, all parties can benefit from increased access to data. This will illuminate what’s happening across the supply chain. Decision-makerscan spot single points of failure and make informed choices about how to manage any disruption.
Finally, when coming out of the crisis, companies and governments should take a complete look at their supply-chain vulnerabilities and the shocks that could expose them much as the coronavirus has.
Organizations should build financial models that size the impact of various shock scenarios and decide how much “insurance” to buy through the mitigation of specific gaps,such as by establishing dual supply sources or relocating production. The analytical under pinnings of this risk analysis are well understood in other domains, such as the financial sector—now is the time to apply them to supplychains.
Triaging the human issues facing companies and governments today and addressing them must be the number-one priority, especially for goods that are critical to maintaining health and safety during the crisis. As the coronavirus pandemic subsides, the tasks will center on improving and strengthening supply-chain capabilities to prepare for the inevitable next shock. By acting intentionally today and over the next several months, companies and governments can emerge from this crisis better prepared for the next one.
When COVID-19 is brought under control we can all breathe a collective sigh of relief, but we mustn't be naïve about the fact that something similar will happen again. In our globalized world, the next disruption is just around the corner so it’s imperative that businesses don’t rest on their laurels.
#Coronavirus #SupplyChain #resilience
Source : Mckinsey,Dun& Bradstreet
Talk to us today to know how our solutions can accelerate your digital transformation
Let's Talk