Envision
"Revolutionize Your Operations with a Conditional Monitoring System: The Future of Proactive Maintenance"
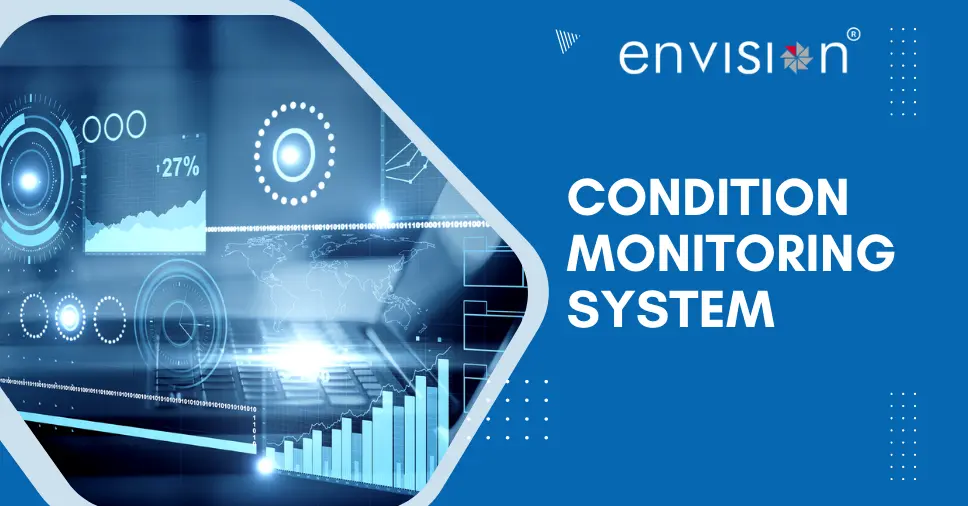
Table of content
1. Introduction
2. Lack of a proper condition monitoring system can lead to a variety of issues
3. Benefits of Condition Monitoring System
4. Conclusion
Condition monitoring system is mandated to continuously monitor the health and performance of a machine, equipment, or system, typically in an industrial setting, in order to identify potential problems and faults early on, so that maintenance can be scheduled, and repairs can be made before serious damage occurs.
Lack of a proper condition monitoring system can lead to a variety of issues
Equipment Downtime : Equipment failures may not be detected without a condition monitoring system until they cause significant downtime. This can lead to production delays and revenue loss.
Maintenance Issues : Only when equipment fails can maintenance be performed on a reactive basis. This can be expensive and time-consuming, as repairs may necessitate more extensive work if the equipment has already failed.
Unplanned Repairs : These repairs may necessitate the use of parts or resources that are not readily available. This can lead to extended downtime and higher costs.
Equipment Lifespan : Equipment that is not regularly monitored may experience unnoticed wear and tear, leading to premature failure and a shorter lifespan.
Safety hazards : Faulty equipment can endanger workers and the surrounding environment, resulting in accidents and injuries.
Benefits of Condition Monitoring System
With the help of Condition monitoring systems(CMS) data can be collected on the performance and condition of equipment using a variety of sensors and measurement techniques. This information is then analyzed using advanced algorithms and machine learning techniques to identify patterns and anomalies that may indicate a problem.
A condition monitoring system's data can be used to predict when maintenance is needed, optimize maintenance schedules, and improve the equipment's overall efficiency and reliability.
Early detection of equipment failures : Using conditioner monitoring system, can detect potential equipment failures prior to their occurrence, allowing for early intervention and repairs to avoid costly downtime and repairs.
Predictive Maintenance : with proper use of CMS, we can use data analytics to predict when maintenance is needed, which can help to optimize maintenance schedules and reduce costs.
Improved Equipment Performance : Regular equipment monitoring can identify and correct issues that may be affecting the equipment's performance, resulting in increased efficiency and productivity.
Extended equipment lifespan : A conditioner monitoring system can help to extend the lifespan of equipment by identifying and addressing issues early on, reducing the need for costly replacements.
Increased safety : By identifying potential hazards early on, a conditioner monitoring system can help to reduce the risk of workplace accidents and injuries.
Reduced maintenance costs : Data analytics-based predictive maintenance can help to reduce maintenance costs by allowing for more efficient use of resources like manpower and spare parts.
A superior monitoring system can assist organizations in improving equipment performance, reducing downtime, extending equipment lifespan, improving safety, and lowering maintenance costs, all of which can lead to increased profitability and competitiveness.
Talk to us today to know how our solutions can accelerate your digital transformation
Let's Talk